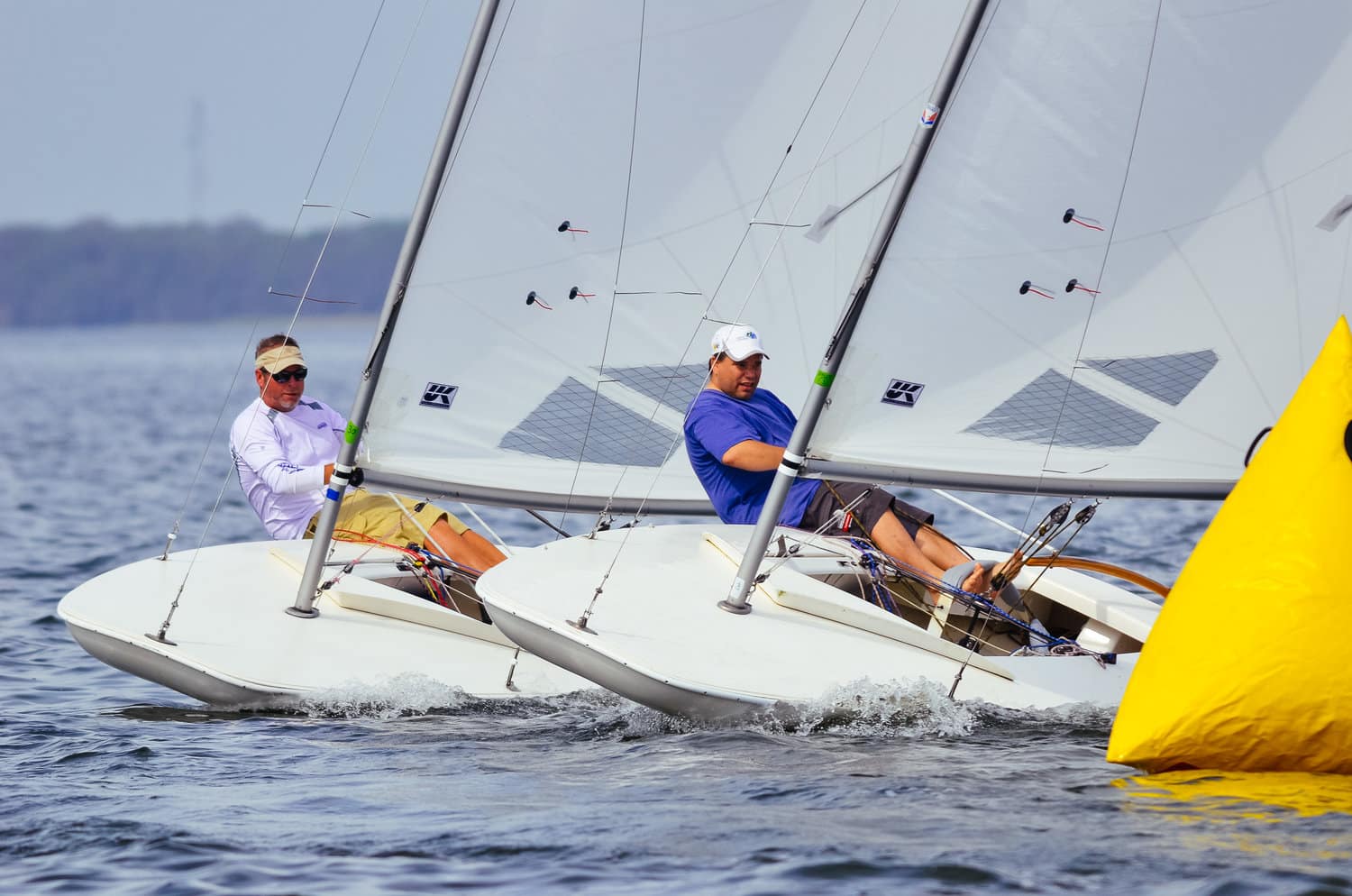
3.1 -Construction Methods
Every sailmaker designs sails on a computer, but the trick is building a sail that will keep its intended shape. UK Sailmakers can offer the option of building sails with the the Tape-Drive® con-struction system as well as with the standard radial and crosscut layouts. This flexibility ensures that you get a durable sail that is custom-designed and built.
You have probably noticed that there is considerable variation in how panels are arranged in modern sails. These variations result from the fact that sailcloth is most resistant to stretch when the yarns are in line with the loads in the sail. Because the loads change direction from place to place within a sail, sailmakers arrange the panels to keep the stronger threadline aligned with the loads, particularly in the leech area where the greatest loading occurs. With smaller, less heavily loaded sails, fabrics can be selected which are adequately strong in all directions, tending to eliminate the need for the more complex and costly panel layouts.
Titanium®
Titanium® sails are made with a grid of continuous carbon loadpath yarns running unbroken between the three corners of the sail; those yarns are laminated between two layers of 3D-shaped film. In the Titanium construction process, the yarns are laid dry–without glue–to reduce weight and to prevent the carbon yarns from becoming brittle.
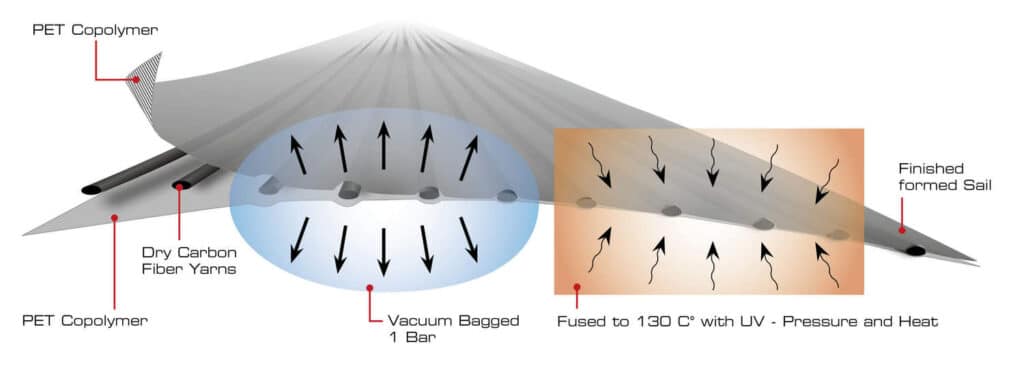
Furthermore, not coating the yarns with glue makes for lighter, more flexible, and more durable sails (by 15-30%), which makes happier foredeck teams and happier owners who are not replacing their misshaped and broken sails as often.
The outer mylar films are the epidermis of the Titanium sail that protect and hold all the layers together. Shiny and weatherproof on the outside, the black or grey PET skins are tacky on the inside from the copolymer coating; this holds the yarns and films in place until the final lamination has been completed.
Uni-Titanium
UK Sailmakers developed Uni-Titanium, membrane sails with sheets of uni-directional carbon added to the continuous carbon fiber yarn layout in a leach to luff orientation, for the greatest shape retention of any sail construction method. The uni-directional carbon sheets used have the thickness of magnetic tape and are just as light. The four layers in a Uni-Titanium sail (Mylar, loadpath yarns, uni-carbon layer and second Mylar layer) are placed in a variable geometry thermo form in which the sail is UV-bonded under vacuum pressure to become a one-piece finished sail. The result is a sail that holds its shape in puffs and lulls. In fact, Uni-Titanium sails hold their shape until a sail trimmer makes an adjustment to change the sail’s shape.
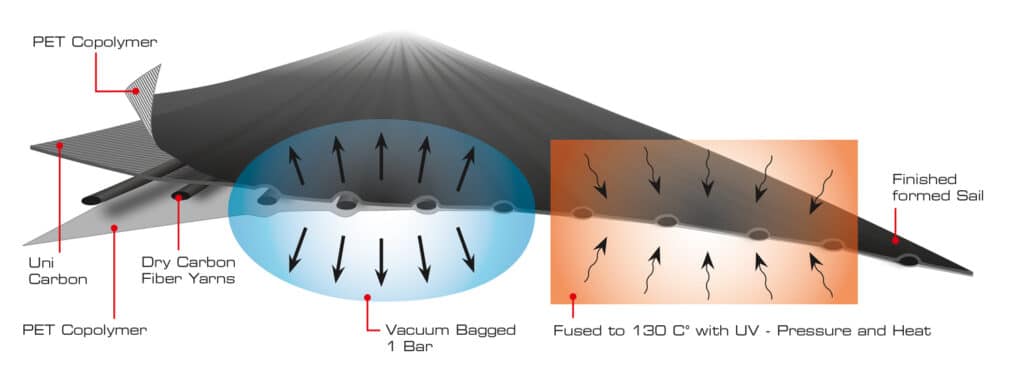
X-Drive
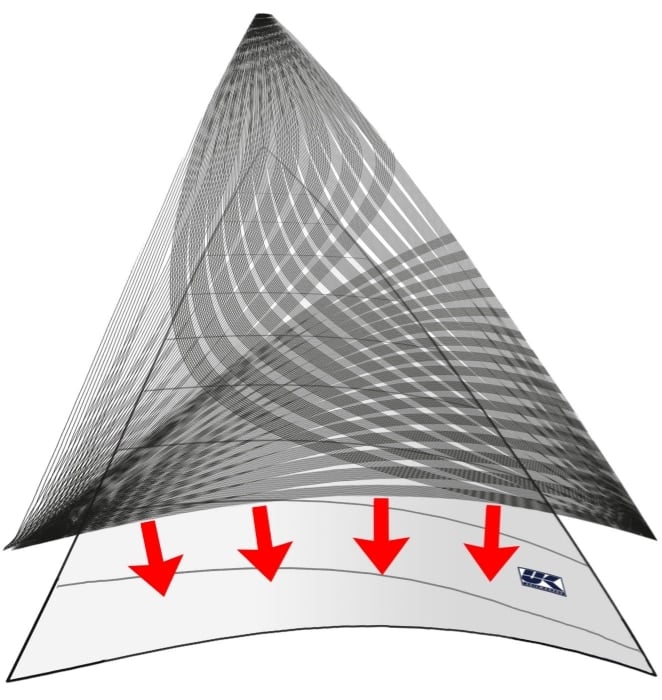
Like Tape-Drive, the X-Drive construction process is a two-part construction method. Sails are made from light weight laminates cut into cross-cut panels that when put together with broad seaming achieve the 3-D shape created by the sail designer. Next the sail is reinforced with a grid of narrow high-strength, low-stretch tapes that are bonded to the sail up to 11 at a time in an 8 inch (20 cm) wide path. Hundreds of closely-spaced yarns are bonded to the sail’s surface for maximum strength and shape-holding. With so many tapes running across the sail, the sail has incredible strength and stretch resistance.
OTHER CONSTRUCTION METHODS
Crosscut Panel Layout:
A sail with all panels parallel to each other and perpendicular to the leech. The cross cut layout is used for traditional mains and genoas because it is simple, does not waste cloth, and it gives sailmakers the most control over sail shape since all the seams are shaped.
Cross-cut sails use fabrics with their greatest strength in the fill direction to withstand the anticipated loading along the leech of the sail since the greatest loads in any sail are up and down the leech. Fill-oriented fabrics are used in cross-cut sails because the stronger fill yarns are parallel to the leech in a cross-cut layout.
Radial Panel Layout:
Radial cut sails are made with long narrow triangular panels called gores which attempt to align the warp thread of the laminate with the primary load paths of a sail. The laminated fabrics used in radial sails have much more strength in the warp direction (that is more yarns or stronger yarns running the full length of the roll of cloth). In order to more precisely match the warp-oriented cloth with the loads in the sail, the gores need to be very narrow. Wide gores are used in low load areas, allowing sailmakers to use cloth more economically.
Radial sails with their many panels allow sailmakers to use more than one laminated fabric in a sail. Stronger laminates can be used in high load areas like the leech and tack, while lighter cloth can be used in the less loaded luff of the sail. A third fabric, one that is heavy-duty and chafe-resistant, can be used in the foot panels to stand up to the abuses of tacking and chafing on the life lines. By mixing cloth types, sailmakers can make a lighter sail that has strength where it is needed.
The gores radiate from the corners of the sail, because all loads start from a corner and then run in arcs through the sail and end at the other two corners.
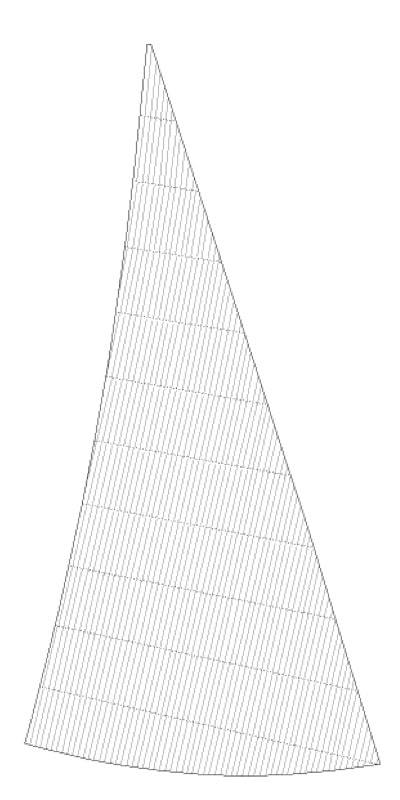
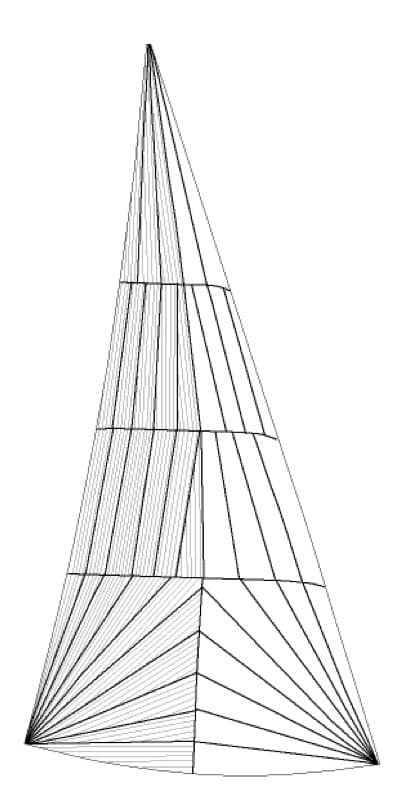